Crafting with Confidence: The Formability and Weldability of 304 Stainless Steel
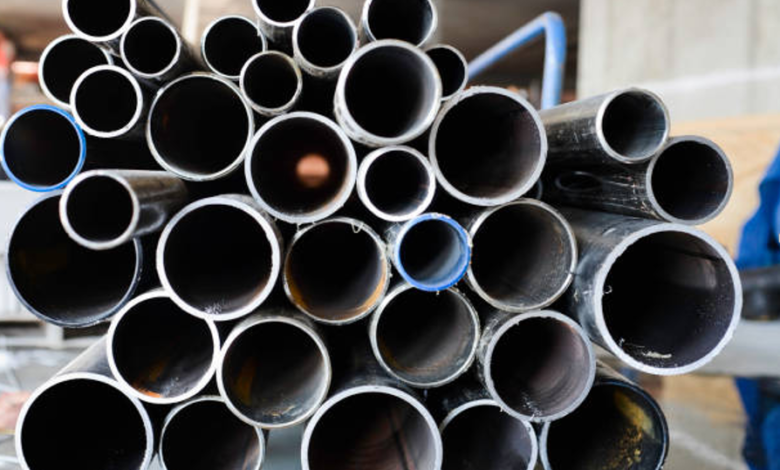
Manufacturing professionals face constant pressure to deliver quality results while managing costs and timelines. Poor material choices can lead to cracked welds, failed forming operations, and expensive rework that destroys project budgets. The wrong steel grade might seem adequate initially, but fabrication challenges quickly reveal its limitations when production demands precision and reliability.
When selecting materials for complex fabrication projects, 304 stainless steel tubes offer exceptional versatility that eliminates many common manufacturing headaches. This austenitic grade combines superior formability with excellent welding characteristics, making it the preferred choice for applications requiring intricate shapes and reliable joints. The material’s balanced composition allows fabricators to achieve consistent results across various manufacturing processes without compromising structural integrity.
Understanding 304 Stainless Steel’s Fabrication Advantages
Superior Formability Characteristics: The austenitic structure of 304 stainless steel provides exceptional ductility that allows for complex forming operations without extensive heat treatment. This characteristic stems from its face-centered cubic crystal structure, which maintains stability during mechanical deformation. Fabricators can achieve deep draws, tight bends, and intricate shapes that would cause other materials to crack or fail.
Deep Drawing Capabilities: Manufacturing components with significant depth-to-diameter ratios becomes achievable when using 304 stainless steel. The material’s work hardening rate provides just enough resistance to prevent thinning while maintaining formability throughout the drawing process. This balance eliminates the need for multiple annealing cycles that add time and cost to production schedules.
Cold Forming Benefits: Room temperature forming operations reduce energy costs and simplify manufacturing processes significantly. The material maintains its corrosion resistance and mechanical properties even after extensive cold working, though some applications may benefit from stress relief treatments. This flexibility allows manufacturers to optimize their production methods based on specific project requirements.
Welding Excellence in Manufacturing Applications
Multi-Process Welding Compatibility: 304 stainless steel adapts to virtually every standard welding technique used in modern manufacturing. TIG welding produces clean, precise joints ideal for visible applications, while MIG welding offers higher deposition rates for structural components. Stick welding remains viable for field repairs and heavy fabrication work.
Filler Metal Selection: Proper filler metal choice ensures joint integrity and corrosion resistance in finished products. 308L filler metal matches the base material’s composition closely, providing consistent mechanical properties across the weld zone. For applications requiring enhanced corrosion resistance, 316L filler metal offers additional protection against chloride environments.
Heat Input Management: Controlled heat input during welding prevents carbide precipitation and maintains the material’s corrosion resistance. Welders achieve optimal results by using lower amperage settings with faster travel speeds, minimizing heat-affected zone width. This approach preserves the material’s inherent properties while creating strong, durable joints.
Production Efficiency Through Material Properties
Reduced Processing Steps: The combination of excellent formability and weldability eliminates many intermediate processing steps that other materials require. Fabricators can move directly from forming to welding without extensive preparation or heat treatment, reducing overall production time. This efficiency translates to lower labor costs and faster project completion.
Consistent Quality Results: Predictable material behavior during fabrication processes reduces the likelihood of defects and rework. The material’s forgiving nature allows operators to maintain consistent quality even when working conditions aren’t perfect. This reliability proves especially valuable in high-volume production environments where consistency matters more than absolute perfection.
Cost-Effective Manufacturing: While 304 stainless steel costs more than carbon steel initially, its fabrication advantages often result in lower total manufacturing costs. Reduced processing time, fewer rejected parts, and minimal post-fabrication treatment requirements contribute to better overall project economics. Smart manufacturers recognize these hidden savings when evaluating material options.
Applications Demanding Superior Fabrication Properties
Architectural Components: Building facades, handrails, and decorative elements benefit from 304 stainless steel’s ability to form complex shapes while maintaining structural integrity. The material’s appearance and corrosion resistance make it ideal for applications where aesthetics matter as much as performance. Fabricators can create intricate designs that would be impossible with less formable materials.
Food Processing Equipment: Sanitary requirements in food processing demand materials that can be formed into complex shapes and welded without creating contamination risks. 304 stainless steel meets these challenges while providing the corrosion resistance necessary for frequent cleaning and sterilization. The material’s non-reactive surface prevents flavor contamination in processed foods.
HVAC System Components: Ductwork, heat exchangers, and ventilation components require materials that can be formed into precise shapes and welded reliably. Temperature cycling and moisture exposure demand corrosion resistance that 304 stainless steel provides naturally. The material’s thermal properties also contribute to system efficiency and longevity.
Quality Control Considerations
Inspection Requirements: Fabricated components require thorough inspection to verify dimensional accuracy and weld quality. Visual examination reveals surface defects and weld profile irregularities that could affect performance. Penetrant testing identifies subsurface discontinuities that might compromise structural integrity over time.
Testing Protocols: Mechanical testing verifies that fabricated components meet design requirements for strength and ductility. Tensile testing confirms that welded joints achieve adequate strength, while bend testing evaluates ductility in formed sections. These tests provide confidence that finished products will perform as expected in service.
Documentation Standards: Proper documentation of fabrication processes ensures traceability and quality control throughout production. Material certifications, welding procedure specifications, and inspection records create a complete quality history for each component. This documentation becomes crucial for applications requiring regulatory compliance or warranty coverage.
Conclusion
304 stainless steel’s exceptional combination of formability and weldability makes it an ideal choice for manufacturers seeking reliable, cost-effective solutions for complex fabrication projects. The material’s forgiving nature reduces production risks while enabling the creation of high-quality components that meet demanding performance requirements. Ready to optimize your next fabrication project? Contact a qualified stainless steel supplier today to discuss how 304 stainless steel can improve your manufacturing processes and deliver superior results.