The Importance and Versatility of Custom Washers in Modern Manufacturing
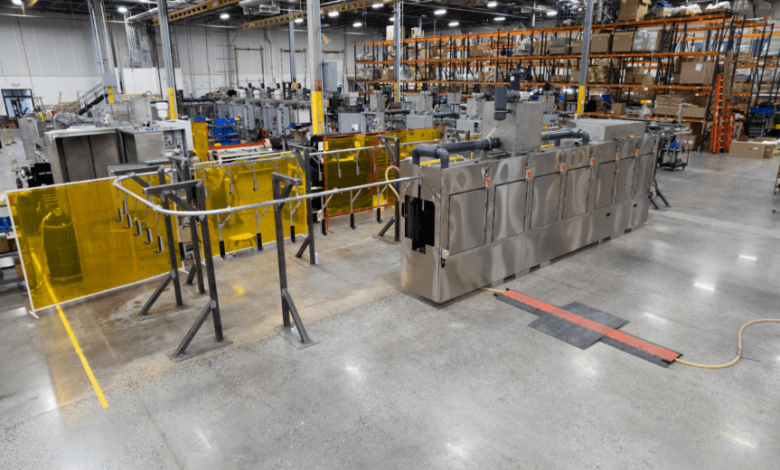
In the vast and ever-evolving world of industrial manufacturing, attention to the smallest components often plays a pivotal role in ensuring product quality and performance. One such component, frequently underestimated, is the washer. More specifically, custom washers have become essential in numerous industries ranging from aerospace and automotive to electronics and medical devices. These small but mighty components offer enhanced precision, improved durability, and tailored solutions that standard washers simply cannot match.
What Are Custom Washers?
At their core, washers are thin plates, typically disk-shaped, used to distribute the load of a threaded fastener like a bolt or nut. However, custom washers go beyond off-the-shelf dimensions and materials. They are designed and fabricated based on exact specifications provided by the client, making them ideal for applications that demand unique shapes, special coatings, extreme tolerances, or specific environmental resistance.
Whether it’s a non-standard diameter, a high-precision thickness, or a complex design geometry, custom solutions are tailored to fit perfectly within a unique assembly, improving reliability and performance.
See also: Revolutionizing Windows: Cutting-Edge Technologies for Modern Homes
Why Industries Choose Custom Washers
The transition from standard to custom washers is driven by various practical and performance-based needs. Below are some reasons manufacturers opt for customized designs:
1. Precision Engineering
In industries such as aerospace, robotics, and medical devices, even a slight dimensional discrepancy can lead to catastrophic failure. Custom-manufactured washers ensure tight tolerances and perfect fitting, helping maintain the integrity of the entire assembly.
2. Material Compatibility
Standard washers are generally made from basic metals like steel or brass. However, many modern applications require materials that can withstand extreme conditions such as high temperatures, corrosive environments, or electromagnetic interference. With custom washers, manufacturers can choose from a wide range of materials including stainless steel, titanium, nylon, PTFE, and even exotic alloys to meet specific requirements.
3. Unique Designs for Special Functions
Certain applications demand unique washer configurations. Examples include wave washers for maintaining load in assemblies with thermal expansion, or conical washers to absorb shocks. With customization, washers can be designed with grooves, teeth, non-circular shapes, or integrated features for enhanced functionality.
4. Corrosion Resistance and Surface Treatment
Custom washers can be coated or treated with finishes like anodizing, zinc plating, or black oxide to enhance their resistance to corrosion and wear. This adds to the longevity of both the washer and the equipment in which it is used.
5. Cost-Effective in the Long Run
While the initial cost of producing custom washers may be higher than using standard ones, the long-term benefits often outweigh the investment. Improved fit, reduced wear and tear, and minimal failures translate into fewer maintenance cycles and less downtime.
Key Applications of Custom Washers
The flexibility and adaptability of custom washers make them suitable for a wide range of industries:
1. Automotive Industry
Custom-shaped washers are used in braking systems, suspension assemblies, and engine components where vibration damping, precise alignment, and temperature tolerance are critical.
2. Aerospace and Defense
Aircraft engines, landing gear, and satellite components rely heavily on precision parts. Custom washers play a crucial role in load distribution and vibration management in these high-stress environments.
3. Electronics
In printed circuit boards (PCBs) and miniature assemblies, thin and precisely machined washers ensure insulation, spacing, and thermal management.
4. Medical Devices
Surgical instruments, diagnostic machines, and wearable medical technologies demand materials that are biocompatible, sterilizable, and corrosion-resistant. Custom washers provide the exact specifications required for safety and efficiency.
5. Renewable Energy
Wind turbines and solar panel structures require durable and corrosion-resistant washers that can withstand harsh weather conditions and continuous motion.
Types of Custom Washers
Different engineering applications require specific washer types, and with customization, any of the following can be adapted to meet unique needs:
- Flat Washers – Basic design, used for load distribution.
- Lock Washers – Designed to prevent fasteners from loosening under vibration.
- Spring Washers – Offer axial flexibility and maintain load.
- Shoulder Washers – Provide electrical insulation and spacing in electronic assemblies.
- Fender Washers – Feature a larger outer diameter for spreading loads over a larger surface.
With modern CNC machining, stamping, laser cutting, and waterjet technologies, manufacturers can produce highly accurate and complex washer designs with ease.
Choosing the Right Custom Washer Manufacturer
When selecting a supplier for custom washers, several factors should be considered:
- Experience and Expertise: Choose a company with a proven track record in custom parts manufacturing across diverse industries.
- Material Selection Capabilities: Ensure the manufacturer has access to a broad spectrum of materials and understands their properties.
- Precision Engineering Tools: The supplier should be equipped with modern technologies such as CAD software, CNC machines, and quality assurance systems like ISO certifications.
- Customization Support: Look for flexibility in design modifications, prototyping, and batch size options.
- Lead Times and Costing: Evaluate how quickly the supplier can turn around your order and whether their pricing aligns with your budget.
Future Trends in Custom Washer Manufacturing
As technology advances and product designs become more intricate, the role of custom washers will only grow. Some future trends to watch include:
- Additive Manufacturing (3D Printing): This will allow for complex geometries and faster prototyping of washers.
- Smart Materials: Integration of materials that react to temperature or stress could lead to self-adjusting washers.
- Green Manufacturing: Emphasis on sustainable and recyclable materials for washer production.
- Automation and AI: Enhanced quality control through AI-based vision systems for 100% inspection of custom parts.
Conclusion
In a world where engineering precision and reliability are non-negotiable, custom washers have cemented their place as indispensable components in modern manufacturing. They offer solutions tailored to specific applications, materials, and design challenges that standard washers cannot address. Investing in high-quality custom parts is not just a matter of preference—it’s a strategic decision that drives performance, efficiency, and longevity in mechanical systems.